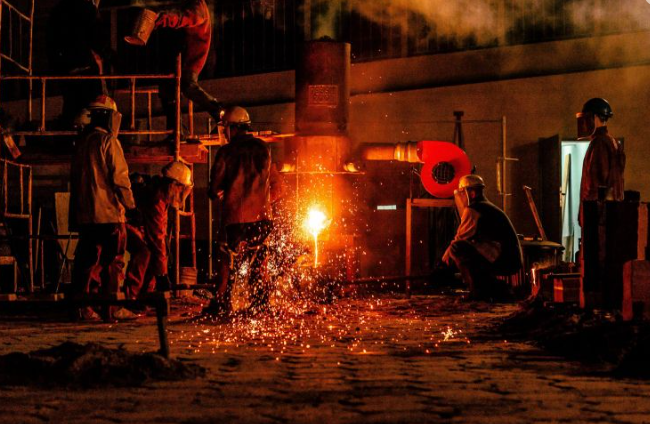
The global steel market exhibiting a growth rate (CAGR) of 3.02% during 2022-2027. Significant growth in the automotive industry across the globe is creating a positive outlook for the market. But with growth comes a lot of challenges in the steel manufacturing process. Companies in the industry face major challenges with rapid digitalization and unlocking potential in data, shifts in consumer demands, and the attraction of top talents.
Steel industry-Consumer Demands
By the year 2040, consumer demands for product and service standards will be altered drastically by trends affecting everyday lives. The global population will grow by 25% by the year 2040, causing concerns in demand expectations for industries heavily involved in infrastructural developments such as construction and transportation. More than 68% of people will be living in urban areas by the year 2050, therefore the metals industry must meet demands from rapid urbanization. Metals will be vital players in the development of sustainable and smart infrastructures globally as investments in infrastructure are projected to increase along with the growing population and growing middle class.
Talks about potential in digitalization and data
The development of smart factories for automated production to streamline production and support functions will be a giant step for players competing in the field for efficient practices. Investment in digital technologies will be a vital step in promoting effective virtual work to enhance actions across operations ranging from maintenance to customer support functions. The utilization of data in the metals industry will be a disruptor in the valuation of the products and services provided by the industry. Digitally-integrated products and services will become the new norm. Skills in IT and digital technologies will become a vital requirement across industries in order to manage highly valuable IT infrastructures and digital functions.
Acquisition of talent –
With developing technologies and evolving working cultures, talent acquisition for top talents is a constant challenge in the eyes of employers. This is a current issue in the metals industry that will carry on into the future – especially with talent with modern technologies for functions such as plant management and maintenance. Industries like metals must make strong efforts in building reputable brands for employment that meet the desires of the potential talent for future generational challenges.
With all these challenges in place, steel and metal industries must look into the future in order to maintain the assets, have proper data management in place, and with a talent shortage, more automation should be there for increasing operational efficiency. Some of the ways by which steel industries can improve their manufacturing plants are listed below
Predictive Maintenance vs Prescriptive maintenance
Due to the mass automation of the smart metals plant, physical access to the plant is mainly required in order to maintain equipment and machinery. Utilizing artificial intelligence, maintenance can be scheduled according to the production schedules onsite, reducing lag time and delays. Immediate repairs that may cause halts to production can be communicated and coordinated between onsite engineers and digital control managers. Onsite or offsite, maintenance can be assisted digitally from start to finish. For example, with the use of Vibration sensors and Edge devices, employees can receive real-time assistance and guidance about the machine’s health and the actions needed to be taken. These tools provide step-by-step instructions and guidelines required in order to carry out maintenance operations – they will guide employees through what maintenance work needs to be done and in what order in order to ensure efficiency and prevent mistakes. As the maintenance is managed digitally, data will be collected on maintenance processes and improved automatically.
Digitalization and Data Integration
With rapid digitalization in the metals industry, the organization must be able to manage a vast amount of data collected throughout the entire production process and the ecosystem surrounding the plant. Integrating collaborative data management into the metals production cycle is imperative in managing production cycles, shipments, resource management, and maintenance of equipment and machinery in order to develop a streamlined production process. For eg with the help of Vibration sensors, the steel manufacturers read the data in real-time and analyze the anomaly using various AI/ML methods. Based on the data and insights from the expert’s team, the team can take necessary actions based on the data provided to alert the users and take proactive actions to reduce unplanned downtimes.
Benefits of the steel industry
According to McKinsey, predictive maintenance usually decreases between 30 to 50% of equipment downtime in industries. In the context of the steel industry, which is involved by a giant chain of industries that demand its product, this data alone shows the value to reduce failures and delays in operation.
The prediction models make it possible to act on equipment even before it fails and needs an unplanned stop, increasing its useful life and the mean time between failure. As a direct consequence of these benefits, the OPEX spent on operation and maintenance in these industries is significantly reduced.
Moreover, failure prediction avoids rework by the operators and unnecessary exposure to the hostile environment of the steel industry, since it is possible to prioritize and assertively understand which are the critical points of the operation that really need attention at the moment.
In general, adopting the predictive maintenance process allows a greater knowledge of the operation as a whole, greater safety for workers in the field, and cost reduction in maintenance and replacement of components or equipment.
- Real-time monitoring of critical equipment’s health
- Prioritizing and planning maintenance before catastrophic failure
- Reduce the risk to safety operators with remote monitoring
- Reduce planned downtime and eliminate unplanned downtime
- Reduce process and quality-related issues
- Increase equipment efficiency and reduce carbon emissions
Final Outcome
Due to the harsh environment present in steel industries and lack of digitalization of processes, the operation ends up becoming more dangerous to workers and presenting several difficulties in its optimization.
In this case, predictive maintenance allows to understand the best moment to act in a process, perform the exchange of a part and even the complete replacement of an equipment, and all this with a much greater anticipation and early planning, reducing spending on rework and increasing the profits of the operation.